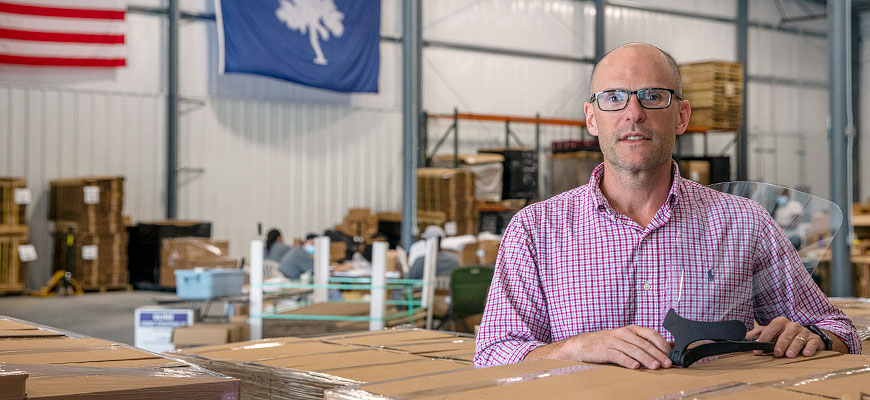
UofSC alumnus’ company makes millions of face shields for health care workers
New shields produced by ZVerse will help service industry workers
Posted on: June 16, 2020; Updated on: June 16, 2020
By Megan Sexton, msexton@mailbox.sc.edu
John Carrington admits he was something of a skeptic when he first heard about COVID-19, believing the coronavirus wouldn’t cause too much disruption in South Carolina.
But by mid-March, that had changed. Carrington, a University of South Carolina alumnus and founder and CEO of ZVerse, a digital manufacturing technology company based in Columbia, started receiving messages from doctors, hospital administrators, nurses and parents of nurses. All were concerned about the lack of personal protection equipment needed to keep health care professionals safe during the pandemic.
“We started getting a lot of direct personal messages from people in hospitals in New York and here locally. That’s for me when it turned,” he says. “You think of doctors as people who have everything under control. I did not get that sense. I told my wife, ‘These people are really scared, and that scares me.’ We were getting a view into hospitals you didn’t always get from the news. That changed it for me and my company. Our entire team was getting personal, emotional pleas from medical professionals.”
ZVerse, a small company known for making 3D printing software, quickly shifted gears and became an important player in the fight to stop the spread of the coronavirus. By early June, ZVerse had produced and shipped 4 million reusable protective face shields for health care workers, with orders being filled for 3 million more. The shields are shipped from the company’s manufacturing plant in Columbia to federal, state and local offices and hospital systems coast to coast, including the U.S. Department of Veterans Affairs, which operates the country’s largest health care system.
The company he started in March 2013 already had a reputation for quickly turning ideas into manufactured products, but the demand for the medical shields was on a different level. Carrington says ZVerse took orders for 3,000 the first day, 10,000 the next, 50,000 the next — all from different places and all without advertising.
“After the first few days, we had orders of 60 to 70,000 shields. I knew then that we couldn’t meet the demand with 3D printing, we had to move to injection molding.”
Injection molding allowed ZVerse to create a large number of shields at a lower price for consumers. Product development for something like this typically takes six months; the company had the first run complete in 14 days.
“We accelerated the product development and just prayed the investment we were making was the right one. There are a lot of upfront engineering costs in injection molding. You have to get it right on the front end,” he says. “We were making a bet. It could have been negative for us if we’d made some wrong decisions in the design.”
It worked, and the company’s growth exploded, making it the largest manufacturer in the country of reusable protective face shields, says Carrington, who earned his degree in advertising from the School of Journalism and Mass Communications.
As the orders and need for virus protection continues to grow, ZVerse has introduced a new generation of protective face shields for workers in service industries, including restaurants, retailers, salons, grocery stores, food plants and the elective medical sector.
You think of doctors as people who have everything under control. I did not get that sense. I told my wife, ‘These people are really scared, and that scares me.’
John Carrington, founder and CEO of ZVerse
The company now is manufacturing and has a patent pending for a new type of shield, the ZShield Flex. Unlike the health care shields which mount to a person’s head, the ZShield Flex has an adjustable neck mount, meaning it hangs around a person’s neck. The shield can flip up when it is needed for face-to-face contact and can stay down when it’s not needed.
Think of it as “a wearable sneeze guard,” Carrington says.
Unlike the original shield, which was made for health care professionals working in hazardous environments, the new shield is designed for people working in restaurants, offices, schools, grocery stores, salons and other environments where customers are served.
“We were trying to come up with something comfortable for the user, that would provide protection and a barrier whether they are handling food or in front of a customer,” Carrington says. “The requests from businesses were different from health care. In health care, they are concerned for their life. Businesses are concerned for their economic life. It was just as emotional for them.”
The company had pre-orders for 100,000, coming from all sectors including dental offices, restaurants, hair salons, schools and retail shops. Before the pandemic, ZVerse had about 24 employees; that’s doubled to about 50, with plans to add another 50 jobs in the coming year, Carrington says.
“Initially, we wanted to help our local community. It was an emotional time for a lot of people in our community. It quickly became a way to direct our energy; to do something positive while everything was in disarray,” he says. “It’s been transformational for our business. And our core business has increased because of this. People now say, ‘How did this small team stand up and have this sort of effort that quickly? If they can solve problems like this, what can they do for us?’ ”
Share this Story! Let friends in your social network know what you are reading about